What are the types of Conductors used in Overhead Power Lines…
- It has maximum electrical conductivity
- It has high tensile strength so that it can withstand mechanical stresses
- It has least specific gravity i.e. weight / unit volume
- It has least cost without sacrificing other factors
- It has lesser cost than copper.
- It offers larger diameter for same amount of current which reduces corona.
- It has lesser conductivity
- It has larger diameter which increase surface area to air pressure thus it swings more in air than copper so larger cross arms required which increases the cost.
- It has lesser tensile strength ultimately larger sag
- It has lesser specific gravity (2.71gm/cc) than copper (8.9 gm/cc) cc = cubic centimeter
- Due to lower tensile strength aluminium is used with some other materials or its alloys
- It has lesser strength and more sag per span length than any other category
- Therefore, it is used for lesser span i.e. it is applicable at distribution level
- It has slightly better conductivity at lower voltages than ACSR i.e. at distribution level
- Cost of ACSR is equal to AAC.
- It is cheaper than AAAC but pro to corrosion.
- It is most expansive.
-
- It has same construction as AAC except the alloy.
- Its strength is equal to ACSR but due to absence of steel it is light in weight.
- The presence of formation of alloy makes it expensive.
- Due to stronger tensile strength than AAC, it is used for longer spans.
- It can be used in distribution level i.e. river crossing.
- It has lesser sag than AAC.
- The difference between ACSR and AAAC is the weight. Being lighter in weight, it is used in transmission and sub-transmission where lighter support structure is required such as mountains, swamps etc.
- It is used for longer spans keeping sag minimum.
- It may consist of 7 or 19 strands of steel surrounding by aluminium strands concentrically. The number of strands are shown by x/y/z, where ‘x’ is number of aluminium strands, ‘y’ is number of steel strands and ‘z’ is diameter of each strand.
- Strands provide flexibility, prevent breakage and minimize skin effect.
- The number of strands depends on the application, they may be 7, 19, 37, 61, 91 or more.
- If the Al and St strands are separated by a filler such as paper then this kind of ACSR is used in EHV lines and called Expanded ACSR.
- Expanded ACSR has larger diameter and hence lower corona losses.
-
- It is 100 % pure conductor and it is standard for reference.
- For 36 kV transmission and above both aluminium conductor steel reinforced (ACSR) and all aluminium alloy conductor (AAAC) may be considered. Historically ACSR has been widely used because of its mechanical strength, the widespread manufacturing capacity and cost effectiveness.
- From a materials point of view the choice between ACSR and AAAC is not so obvious and at larger conductor sizes the AAAC option becomes more attractive. AAAC can achieve significant strength/weight ratios and for some constructions gives smaller sag and/or lower tower heights. With regard to long-term creep or relaxation, ACSR with its steel core is considerably less likely to be affected.
- Jointing does not impose insurmountable difficulties for either ACSR or AAAC types of conductor as long as normal conductor cleaning and general preparation are observed. AAAC is slightly easier to joint than ACSR.
- Historically there has been no standard nomenclature for overhead line conductors, although in some parts of the world code names have been used based on animal (ACSR – UK), bird (ACSR – North America), insect (AAAC – UK) or flower (AAAC – North America) names to represent certain conductor types.
- Aluminium-based conductors have been referred to by their nominal aluminium area. Thus, ACSR with 54 Al strands surrounding seven steel strands, all strands of diameter d 3.18 mm, was designated 54/7/3.18; alu area 428.9 mm2, steel area 55.6 mm2 and described as having a nominal aluminium area of 400 mm2.
Why Lighting transformers are used ?
(2 Min Read)
- Lighting Transformers are designed to supply power to lighting equipment in a commercial / industrial / domestic unit.
- Lighting transformers serves as isolation between primary and secondary, it also restricts any high voltage spikes and EMF coming with the raw mains incoming power.
- The prime reason for using Lighting transformer is to reducing the fault level of the lighting installation where the wires/switch gears used would have a lesser short time withstand rating.
- Another reason is to isolate the other loads like motors etc from lighting loads which basically operate on single phase supply and hence prone to unbalance as well as ground faults. so its better to use a isolation transformer having ration 1:1, it will provide the complete isolation to the equipment which is connected to PCC/MCC.
- It is also used where incoming supply is 3 phase 3 wire and lighting load is 220 Volt single phase.
Why Relay often has two ratings AC and DC...? How to choose the correct one ...???
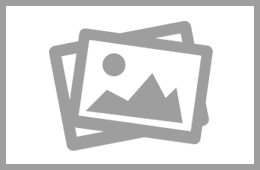
The contacts in a relay (and the same is true for other switches) have to be able to safely and repeatedly allow and interrupt the rated current.
Interrupting is hard on the contacts, since there is always some inductance in the circuit, which creates a high voltage when the current is interrupted. This voltage causes a spark (continued current flow) when the contacts open, and gradual damage to the contact surfaces. If the contacts are too close, and the circuit can supply a high enough voltage, the spark may continue a long time.
In DC circuits the spark is only extinguished when the contacts are far enough apart. The higher the voltage of the circuit, the bigger the contact gap has to be. In AC circuits this spark stops naturally because voltage and current reduce to zero twice per AC cycle, so for a given contact separation a much higher circuit voltage can be tolerated.
How to calculate for the Correct Relay
Relay Ratings and Limits
Relays often have two ratings: AC and DC. These rating indicate how much power can be switched through the relays. This does not necessarily tell you what the limits of the relay are. For instance, a 5 Amp relay rated at 250 VAC can also switch 10 Amps at 125VAC. Similarly, a 5 Amp relay rated at 48 VDC can switch 10 Amps at 24VDC, or even 20 Amps at 12VDC.
Volts x Amps = Watts - Never Exceed Watts!
An easy way to determine the limit of a relay is to multiply the rated Volts times the rated Amps. This will give you the total watts a relay can switch. Every relay will have two ratings: AC and DC. You should determine the AC watts and the DC watts, and never exceed these ratings.
Example Calculations:
AC Volts x AC Amps = AC Watts
DC Volts x DC Amps = DC Watts
Example:
A 5 Amp Relay is Rated at 250 Volts AC.
5 x 250 = 1,250 AC Watts
Example:
A 5 Amp Relay is Rated at 24 Volts DC.
5 x 24 = 120 DC Watts
If you are switching AC Devices, Make Sure the AC Watts of the Device you are Switching DOES NOT Exceed 1,250 when using a 5A Relay.
If you are switching DC Devices, Make Sure the DC Watts of the Device you are Switching DOES NOT Exceed 120 when using a 5A Relay.
Resistive and Inductive Loads
Relays are often rated for switching resistive loads. Inductive loads can be very hard on the contacts of a relay. A resistive load is a device that stays electrically quiet when powered up, such as an incandescent light bulb. An inductive load typically has a violent startup voltage or amperage requirement, such as a motor or a transformer.'
Startup and Runtime Loads
Inductive loads typically require 2-3 times the runtime voltage or amperage when power is first applied to the device. For instance, a motor rate at 5 Amps, 125 VAC will often require 10-15 amps just to get the shaft of the motor in motion. Once in motion, the the motor may consume no more than 5 amps. When driving these types of loads, choose a relay that exceeds the initial requirement of the motor. In this case, a 20-30 Amp relay should be used for best relay life.
When the relay opens it will draw an arc. With AC power the current drops to zero 100 or 120 times per second (depending on whether you have 50Hz or 60Hz power), and this will allow the arc to extinguish. With DC power you don't get this automatic interruption, and an opening arc may last longer, burning the contacts in the process. That's why relays are allowed to switch only a fraction of the AC power if DC.
It's not uncommon to see 250V AC relays only rated for 30V DC.